需求和背景资料
深圳某公司生产小型家用电器产品,大部分产品部件需要注塑成型,且有各种不同的形状和颜色,半品部件加工完成后再进行组装。客户基本情况如下:
各种注塑机超过百台
产品品种多,模具多
模具与产品具有多对多的关系
同一种模具可生产多种颜色产品
使用相同模具的产品,可能会使用不同的镶嵌件
部分产品有拼模,即几个产品共用一个模具
主要问题
在导入PlanMate前,排程采用人工方式,有以下问题:
模具的管理不正规,产品与模具的对应关系,模具使用次数、当前状态都靠人工管理,经常处于混乱状态
生产排程只能排出未来24小时,无法排几天后的计划
订单不能给出确定交期,常常延期
颜色切换、模具的切换没有优化,效率无法保证
模具故障、订单变更时需要修改计划,计划修改困难
系统导入后的改善
通过导入PlanMate,客户在设备利用效率、交货期管理等方面都得到极大改善
- 规范化、强制性的数据维护:在人工排程方式下,有多个生管,每人负责一部分设备,每个人都只维护自己需要的数据,没有统一的数据维护管理,在生管请假或辞职时,会造成排程混乱。通过导入PlanMate,因为系统强制要求,由专人负责数据管理,对于产品、模具、颜色、生产工艺参数都有精确的定义,避免了出现因数据错误造成排程错误, 也不会因人员变更产生混乱。
- 节省人力,从多人排程转变为系统自动排程,只需要一个人操作。排程速度快。
- 从只排一天计划到可排全部工单,短期排程1-2周,用于车间实际生产。长期3-6个月的计划,用于订单评估和交期确认,设备负载评估。
- 通过订单交期的精确确认,减少了订单延期,客户满意度增加。
- 快速应对计划的变化,在设备故障或需求变更时,快速重排计划。
- 模具切换、色彩变化在排程时进行优化,减少了不必要的切换,降低了切换成本。通过同色系深浅变化,深浅色分开排程,避免不合理的颜色变化,减少颜色切换造成的时间和色料的浪费。
解决方案要点
- 需求拆分:部分订单是按月下单,量比较大, 如果不进行拆分需要连续生产多日,影响其它订单的生产。
解决方案:在对日交货订单进行产能分析后,根据各周的设备负载,将月订单按照设备负载拆分到周,使各周的负载率均衡。这部分在客制模块PlugIn中实现
- 机台选择:通常一个模具有几种型号机器可选,在出模时间不变的情况下,优选吨位较低的机器,降低生产成本。
解决方案:PlanMate的模型中,每个模具可以选择多个设备,各设备优先级可不同。在模型中定义设备选择优先级后,自动排程中系统会优选优先级更高的设备。
合并生产与切换的优化
- 一模多出:一个模具由几个产品拼合,分别开穴位,排程时要拼在一起生产
解决方案:因为产品的需求时间和需求量可能不同,因此我们设计了匹配扣减功能,让系统按照需求量最大需求量的产品,按时间顺序对其它料号进行匹配扣减,保留需求量最大的产品工单,并根据料号的需求时间进行前后调整,使生产能满足所有工单的交货要求。这部分在客制模块PlugIn中实现。
- 模具和颜色的切换:模具切换增加成本,随意的颜色切换引发产品品质问题,增加切换成本。
解决方案:
-
- 相同产品,需求时间接近的工单,在满足交期的情况下,相同产品会连续排程。使用相同模具的产品,在颜色切换允许的情况下,也会连续生产,减少模具切换。
- 为颜色切换设定时间和成本,定义禁止的切换(例如黑色到白色),则排程时系统会自动优化颜色切换,并避免禁止的颜色。
- 多模具选择:部分产量大的产品会开多个模具,系统排程需要选择模具
解决方案:如果产品只有一个模具,排程不会同时开两台机生产。如果产品有多于一个模具可选,在模型中要定义模具选择优先级,排程时系统按照优先级选择模具。如果只使用一个模具会超过交货期,则系统会同时使用多个模具生产。
- 模具的状态和养护:模具需要定期养护,在此期间不能使用
解决方案:PlanMate的模型允许辅助资源在不同的时间范围内数量不同,在不可用时间段将模具数量定义为0,则在此时间排程中不会使用此模具。
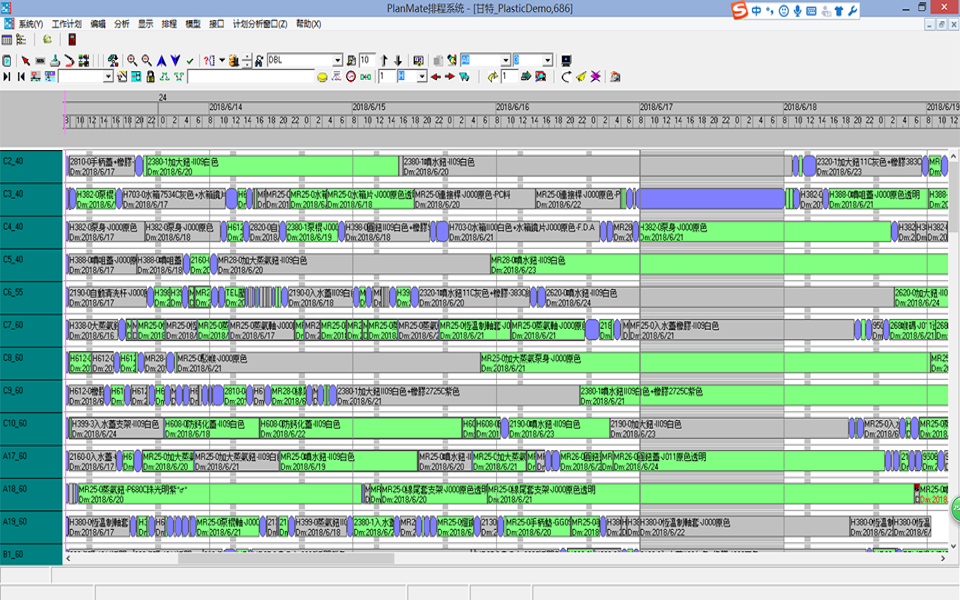
生产进度和计划修改
实际生产进度:在排程后需要获取实际生产进度用于计划的跟踪调整
解决方案:工厂未导入MES系统,使用PlanMate的手机APP在车间,用PAD报工。Planmate读入实际进度,自动更新计划,生管按照实际进度调整计划。
订单调整和计划的修改
正常情况下每天下载新工单,运行一次排程,当前的计划中会有部分工单完结,又有部分新工单加入。
异常情况用户手工调整生产计划
生产排程报表
解决方案:生产排程报表采Excel 中的VBA方式定制,格式灵活且易于扩充,输出的报表可以作为独立文件分发并可以编辑修改。报表主要包括几种:?
车间使用的按班次分拆任务的生产计划
- 所有工单的交货日期报表(提前或延迟时间,WIP等)
- 产品每日产出计划
- 物料需求计划
- 在库库存分配计划