对于多分厂/车间计划,PlanMateAPS根据企业的生产规模、BOM结构、生产工艺特点提供不同的解决方案。
组装与零部件的协同排程是生产计划的难点,通常包括多家分厂或者多个独立车间的计划,由不同的生管负责。通常组装计划对应客户需求,零部件生产需要为组装计划供货。通常BOM分多个层级,很多会有虚拟阶,除了虚拟阶,每个层级都单独开工单。
- 各级工单数量不匹配。ERP在开工单的时候,为了简化生产管理,子件工单常常会合并多个需求。另外加工时长也对工单大小有影响,加工时间长的工单数量较小,加工时间短的工单数量较大。经过长期的订单变更、不良报废等因素,各级工单之间很难建立关联关系。
大型ERP会根据BOM结构在各级工单间进行匹配。基本算法如下:
- 成品工单根据订单的交货日期确定需求时间,然后计算开工和完工日期。如果一个工单匹配多个订单,日期按最早的需求设定。
- 半品工单与上级工单匹配,如果一个半品工单匹配到多个上级工单,则按照最早的需求日期计算开工日期
从以上算法可以看出,零部件的生产时间都是以后级工单的最早日期做参考,这就导致很多半品工单生产时间过早。
- 各分厂计划独立,关联性不强。例如注塑厂模具故障,一个零件无法生产,合理的做法是马上通知电子产和组装厂,该产品不要排产,但执行起来又很困难。由于工单没有一一对应关系,零部件由多个产品共用,很难确定哪些订单受影响。
排程的第一步是划分边界,确定计划员的工作范围,划分的原则是边界清晰,计划的复杂程度可控。
第一个需要明确的问题是由几个人负责排产,即如何划分边界。我们不建议创建一个非常复杂的计划。如果设备太多,工序关系复杂,甘特图上如蜘蛛网一样的连线让人无法看清逻辑,会让计划的分析和修改变得异常困难。
虽然APS自动排程,但是生产计划应该在计划员的控制中,生产进度异常和订单变更,设备故障等,都需要人工介入修改计划,因此每个生管负责跟踪的设备数量应该在可控范围之内。
按生产工序分隔方案示例:
- 成品组装
- PCBA
- 注塑成型
- 钣金加工
问题:各生管工作负荷不均衡
按车间区域分隔:
例如一个机加工厂,有4个大车间,每个车间有大约200台设备,则按照车间分隔职责。按这种分配方法,一个产品的各工序不能跨越车间。
问题: 一个产品可能会允许在不同的车间生产,各时间段各车间的负载不均衡。通过产能分析和车间之间的订单分配可以解决。
PlanMateAPS针对不同规模的企业,采用不同的解决方案。
统一排程:对于规模不大的企业,虽然生产分车间+BOM分层,如果设备总数并不多,复杂程度不高,通常可由一名负责排程。系统的方案是进行分级工单匹配,建立工单之间的前后关系,APS根据匹配结果进行排程
BOM结构
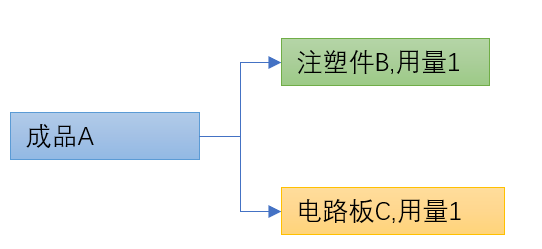
工单清单
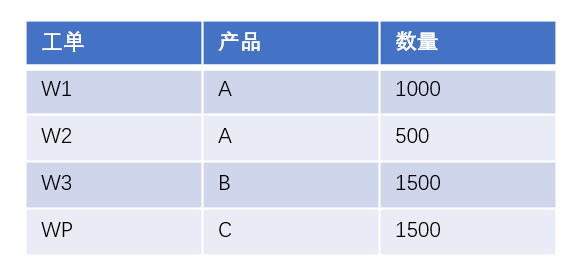
工序排程
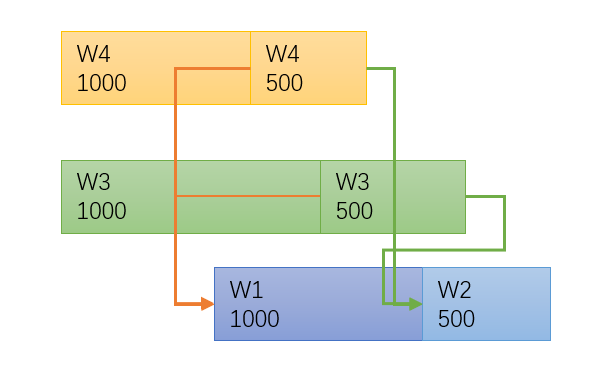
如果是大型企业,上述方案1的工单匹配方法,会导致关联关系过于复杂,逻辑不清晰,超出计划员的可控范围。
对于大型企业,在边界划分后,多个计划员独立排程。APS根据BOM结构在多个计划之间建立互相约束的关系。
- 零部件的产出计划转换为在途库存,组装使用在库+在途库存约束排程。
- 此种方式前工序需要有一定的锁定时间,假定在锁定期内,半品生产计划已经确定,不方便修改,在锁定时间内,使用物料约束排产。在锁定时间后,按需求日期排产
分级计划示意图
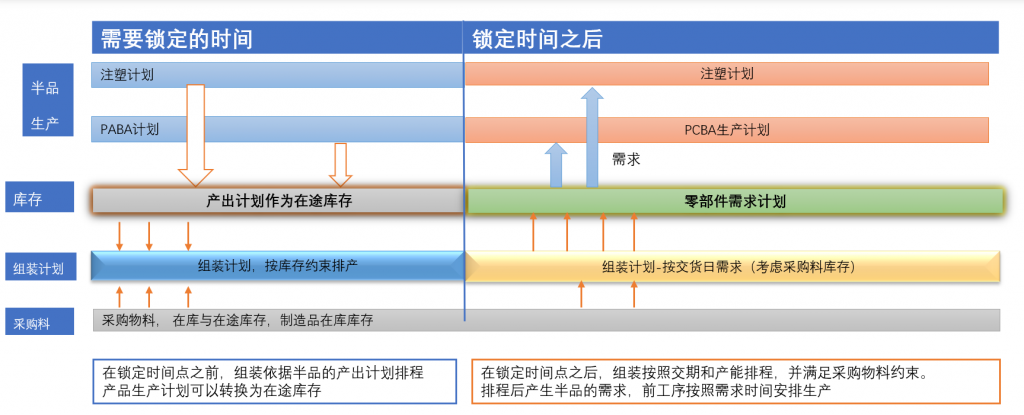
多工序协同工作流程
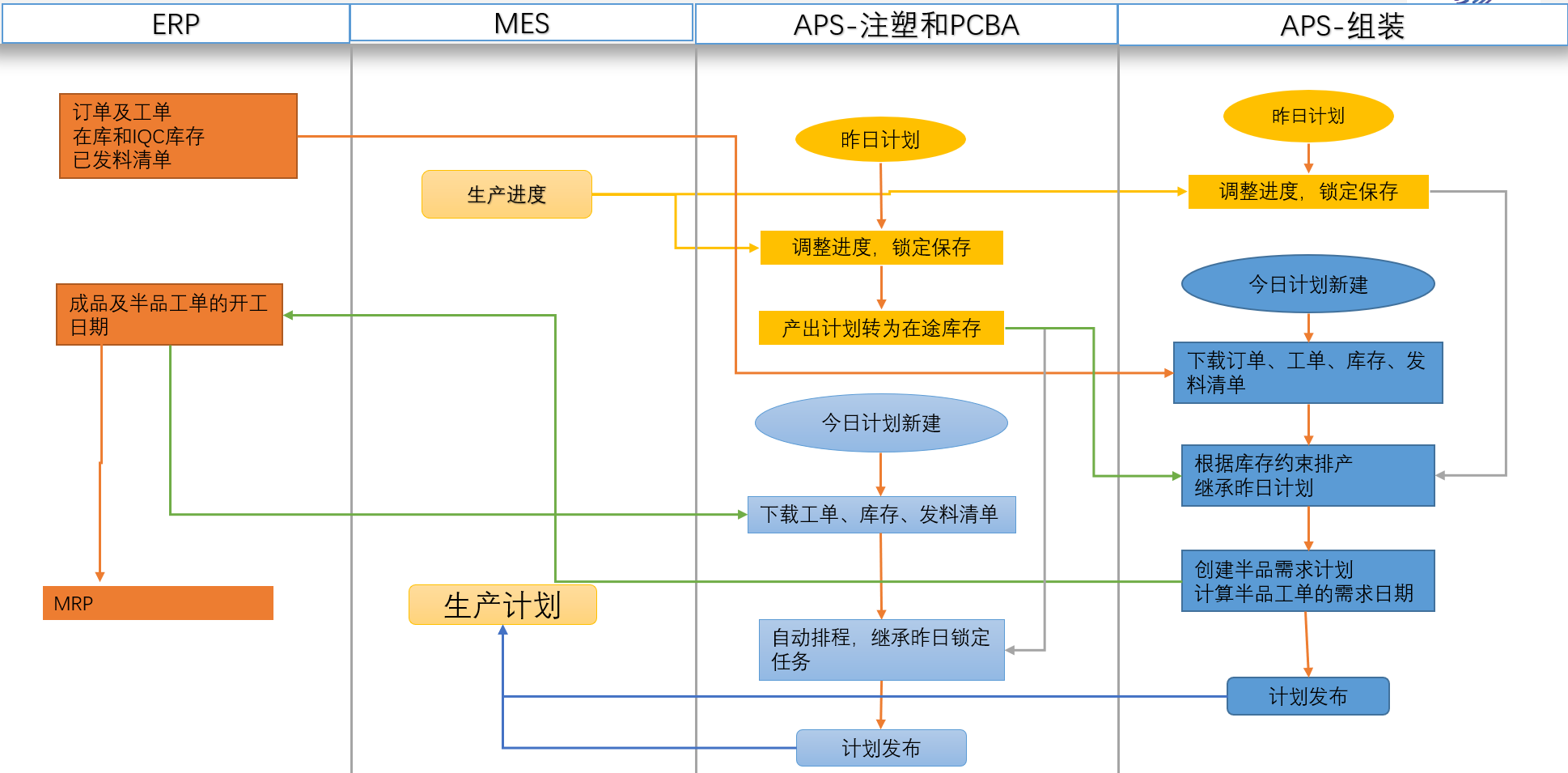
相关资讯
了解更多APS知识